Making mosaic pendants
One of the things I love most about my job is designing mosaic pendants from super sparkly dichroic glass. The lack of events and festivals during our 2020 Covid summer gave me the opportunity to create some new designs.
Eva Glass Design brightly coloured mosaic pendants
Dichroic glass
Dichroic glass has a unique property of reflecting one colour while transmitting another. This makes the colours of the finished piece change when it moves and means every single piece is completely unique.
Dichroic glass is manufactured by spraying a thin chemical film onto the glass in a vacuum chamber, making it one of the most expensive glasses to produce. It was actually developed originally by NASA as dichroic filters for use in space travel. These filters which have the same property of simultaneously transmitting and reflecting light protect spacecraft instruments from cosmic radiation. Then of course glass artists and jewellers became aware of them and a whole new market was created!
The making process
I make mosaic pendants using very small pieces of dichroic glass fired onto a black background. I try to use up small offcuts as much as I can, and it can be a very fiddly job as many pieces are just a few millimetres in size. I don't follow any particular pattern except for the size of the base layer, but I do use a photo album of previous pendants I've made as a reference of which colours and patterns look the best together.
I've learnt to keep all my different types of dichroic glass clearly labelled. Dichroic glass often changes colour quite dramatically in the kiln, and what goes into the kiln is frequently very different from what comes out! You can see this in the photos below of pink pendants pre-fire and once finished off. After a lot of trial and error, now I always make small test firings at different temperatures to keep a record of how each type of glass fires.
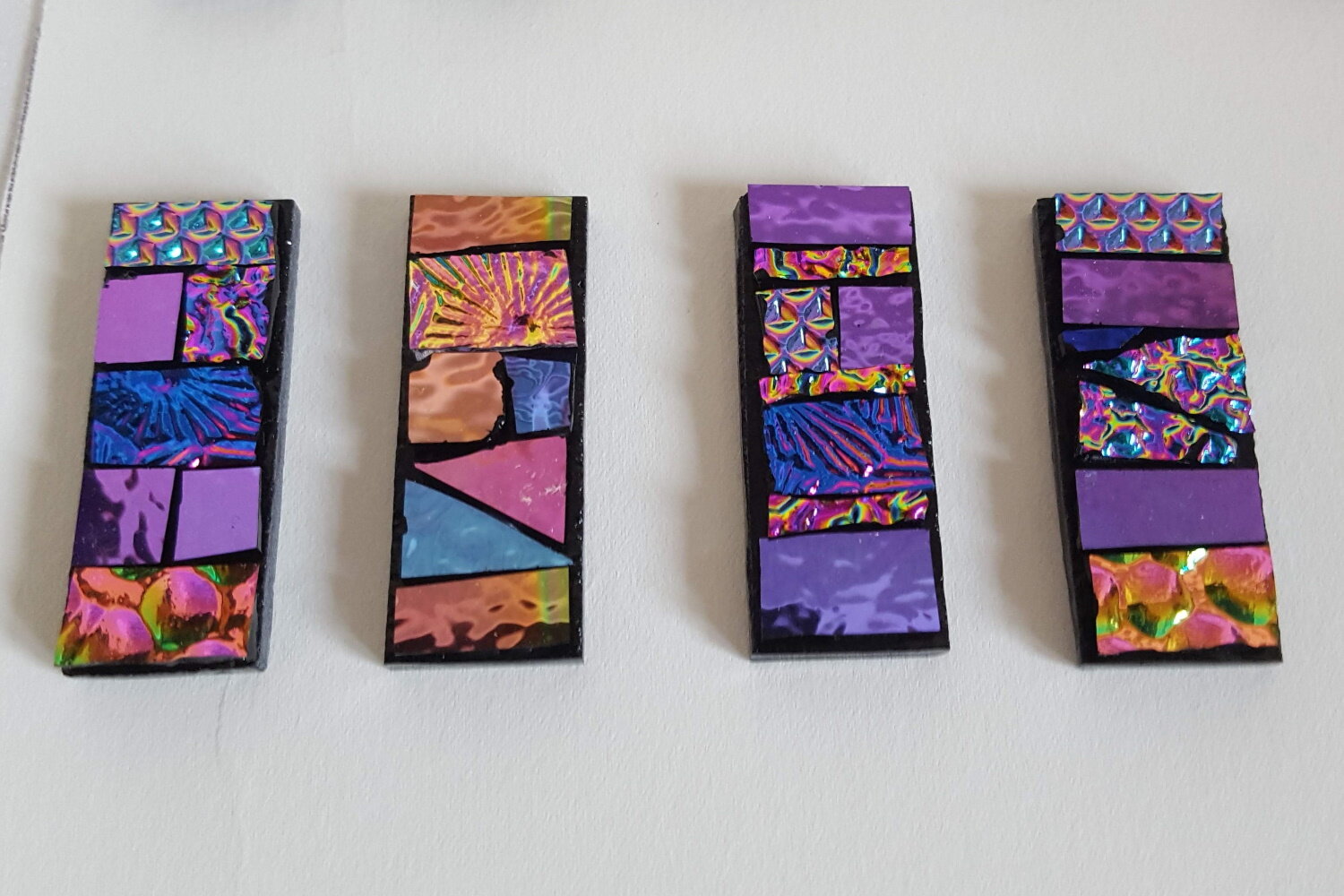
Colour schemes
I usually make mosaic pendants in 3 colour schemes: gold/red, blue/green and pink/purple. Once I'm happy with the design I fire the pieces in my kiln heated to around 750-760C, depending on the effect required. The higher the temperature, the more rounded the edges of the glass become. There is always an element of risk with glass fusing and I never quite know how a piece is going to turn out until I open the kiln. This keeps me on my toes! These pendants are fired on what's called a tack or contour fuse: at about 750C.
Experimentation and development
I've been making these contoured pendants for a few years and they are always very popular, both at the events I go to and with the shops and galleries which I supply. However, for a while I'd been wanting to create mosaic pendants which are capped with a layer of clear glass creating a smooth finish. This is what we call a full fuse, and most of my smaller jewellery pieces are fired in this way.
Our year of Covid-19 has been, to be honest, completely bloody shit for the entire world. However, if it had any benefits for me, its been in creating time for development and experimentation. Usually in the summer I'm so busy taking my stall to events and folk festivals that I don't have the time to experiment with new work, but at least this year I did have that time. I used it well in experimenting with making circular mosaic pendants capped with clear glass in various styles.
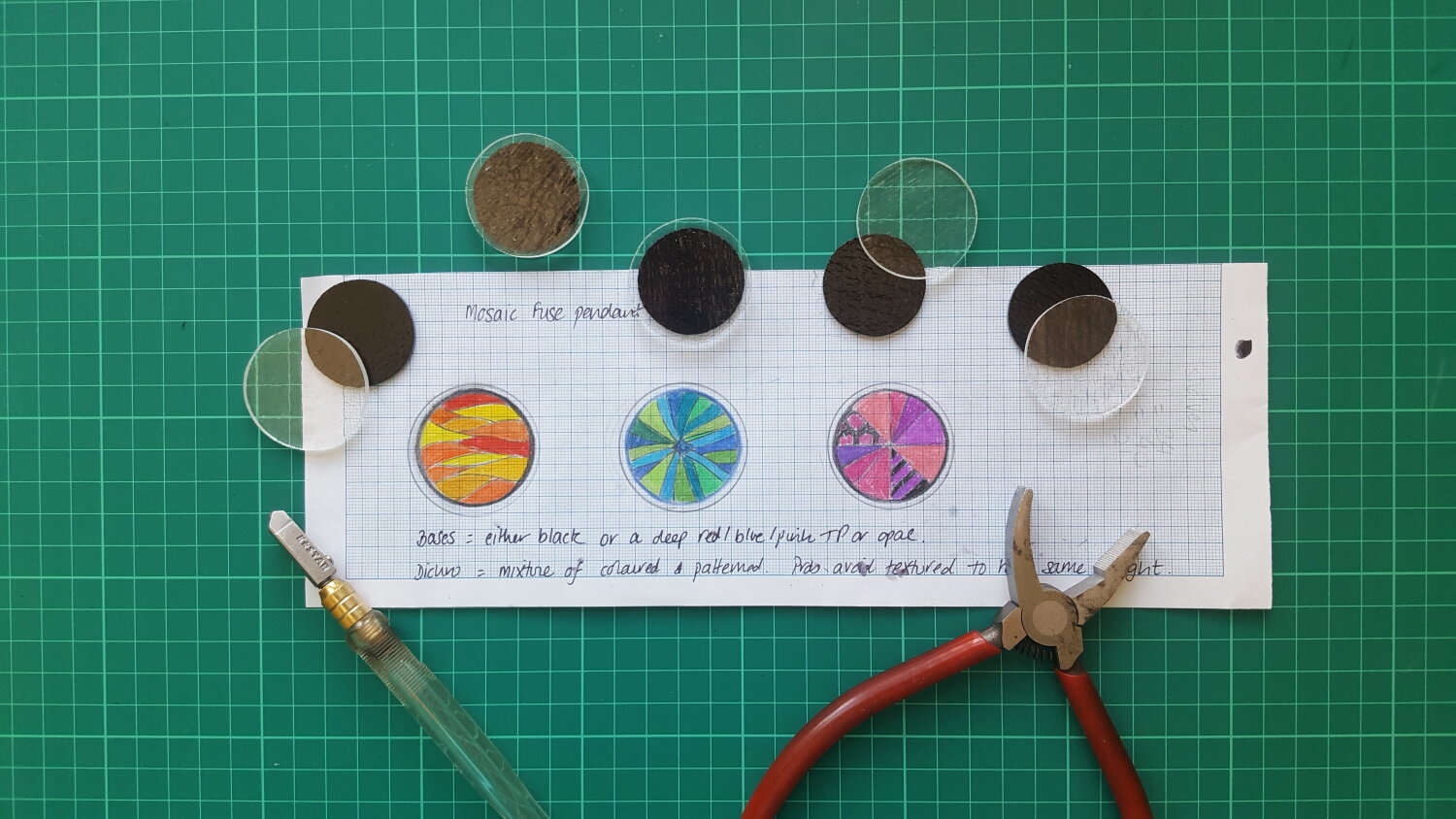
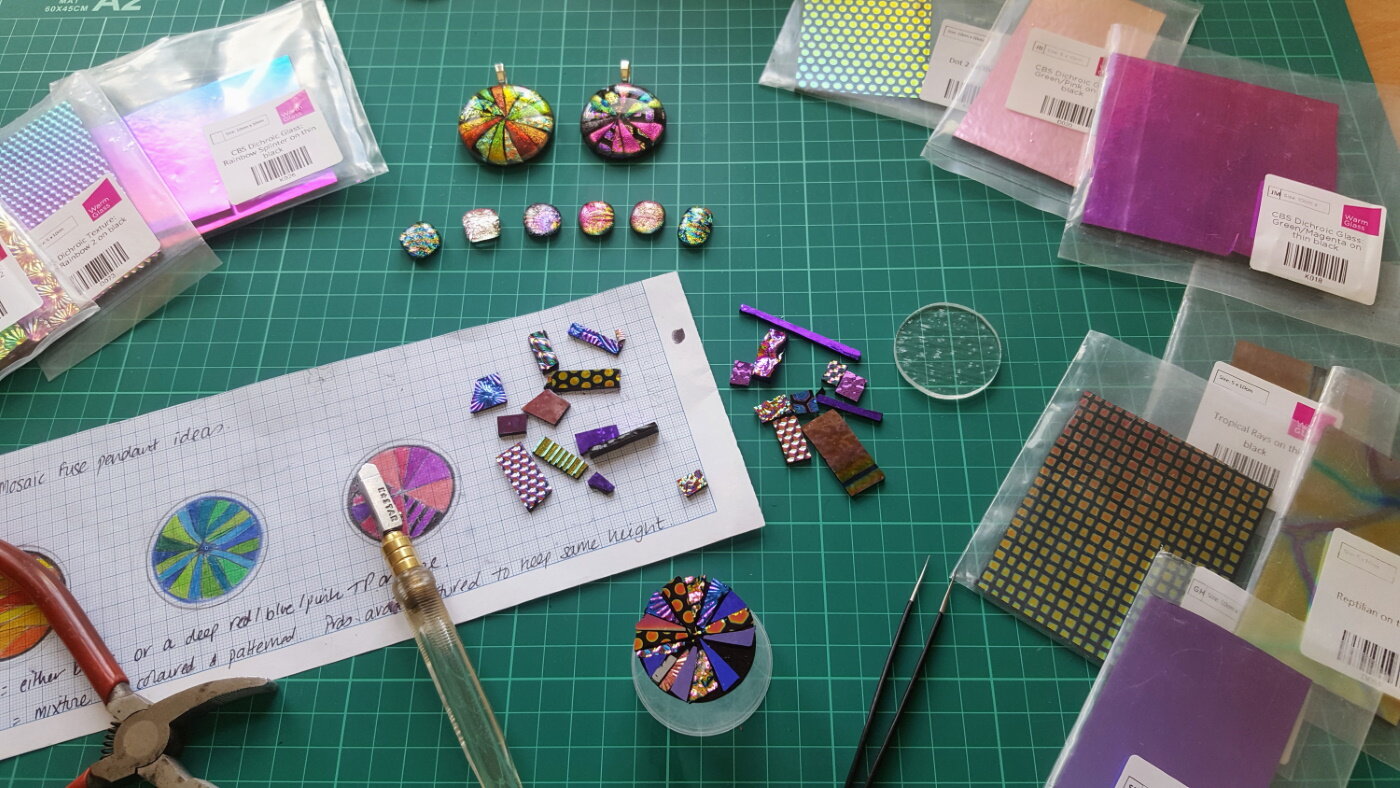
Designing and making circular mosaic pendants and the different styles I came up with.
Pinwheel pendants
From the 3 styles I experimented with I've now launched my new collection of Pinwheel Pendants. These are large circular pendants with the mosaic design radiating out from the centre. Also kind of like a pizza but I didn't think that name had such a good ring to it.
My pinwheel pendants start out as a base layer of black glass and a capping layer of clear glass which is slightly larger. Its much more difficult to cut glass in circles than in straight lines, so even just this bit of the making process takes more time. I then cut thin wedges of dichroic glass and fit them around the black base, using the same three gold/red, blue/green and pink/purple colour schemes. The pendants are capped with the clear layer and fired to a full fuse at around 800C. As the capping glass is slightly larger it overlaps the other 2 layers, holding the seams between the individual pieces of glass together and creating a smooth finish.
Fittings and finishings
I finish all my jewellery pieces with good quality fittings from reputable UK suppliers. All ear wires, studs and butterflies are 925 sterling silver. Pendant bails are silver plated, and each comes with either an 18" leather cord or a silver plated chain. Each piece is presented in an individual box making them ideal gifts for someone special (including yourself!). Sterling silver bails and chains can also be ordered for a commissioned piece.
Pinwheel pendants are available from my Etsy shop www.evaglassdesign.etsy.com and stockists:
Wye Valley Crafts, Tintern
Glass Designs Gallery, Bristol